Project Redshift is AeroNU‘s central rocketry project. The group is entirely student-run, and is working towards competing in DPF, an intercollegiate rocketry competition.
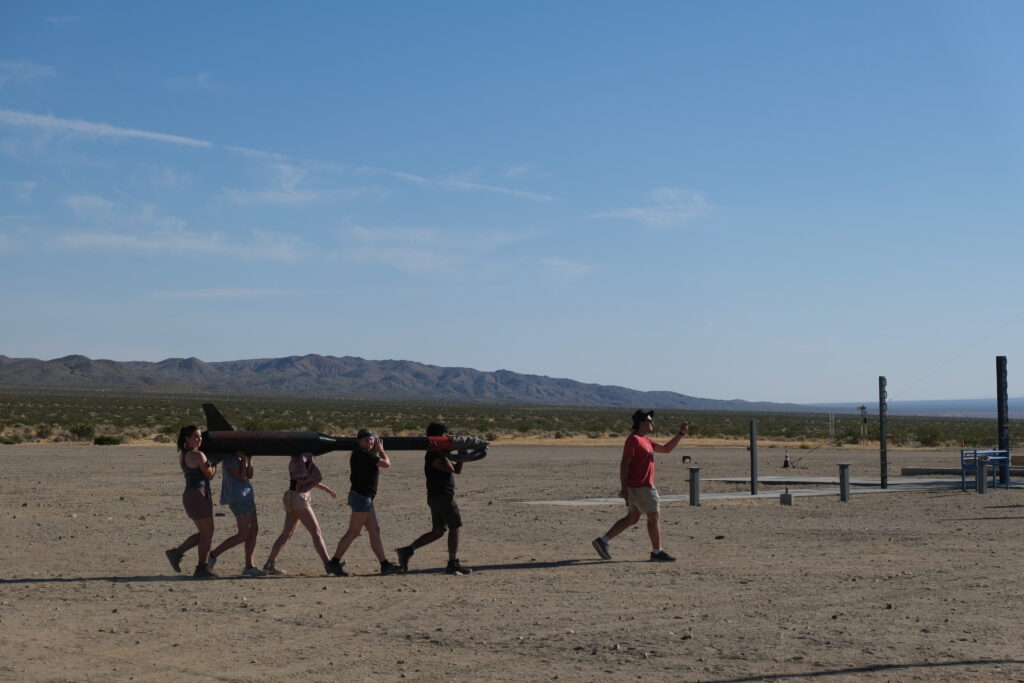
I joined Redshift in the spring of my first year, under the internal mechanics subgroup. I met many talented and kind engineers, and learned a tremendous amount about rocketry. With this group I built an airspeed sensor, and conducted parachute experiments.
I then moved to the propulsion subgroup, who was working on a bi-propellant liquid-fueled rocket engine. I became enthralled with the complexity of this process, involving advanced fluid simulations and combustion calculations.
The liquid propulsion group has made remarkable progress considering it’s only ~4 years old. Our first project made for flight is a regeneratively cooled kerosene-LOX engine (commonly called the regen engine), and uses a pintle injector machined from aluminum in house.
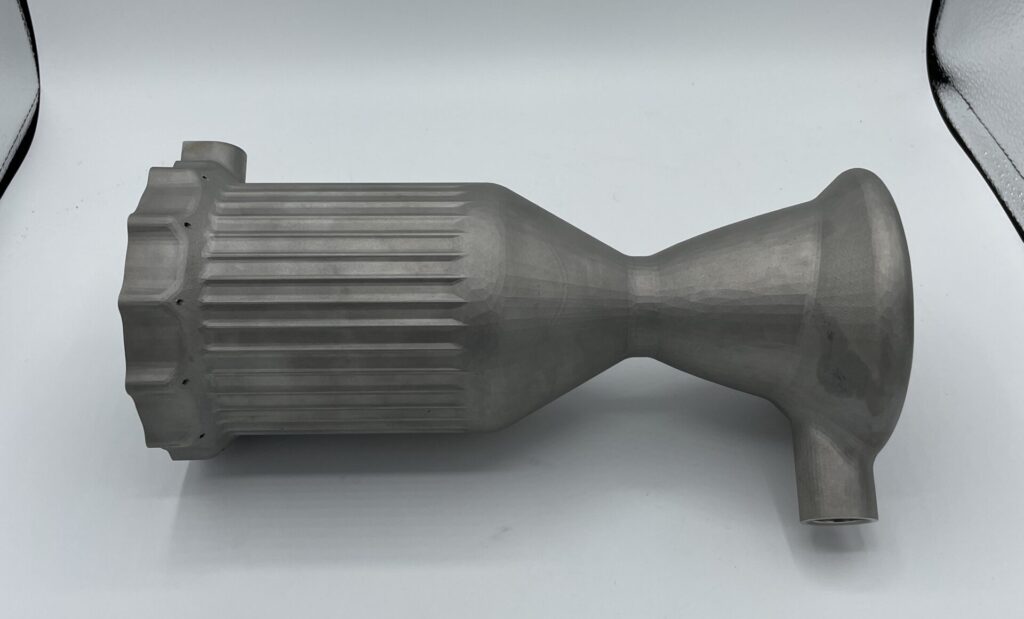
Over my time in propulsion, we’ve been in the testing and validation phase of the regen engine. This includes countless waterflows, cold flows, and 2x static fires to date. These are all performed on our horizontal test stand, a pressure-fed feed system meant for maximum data acquisition. Setup procedures are often at least partly manual, but pressurization and flow is controlled entirely remotely through a pop-up ground-station.
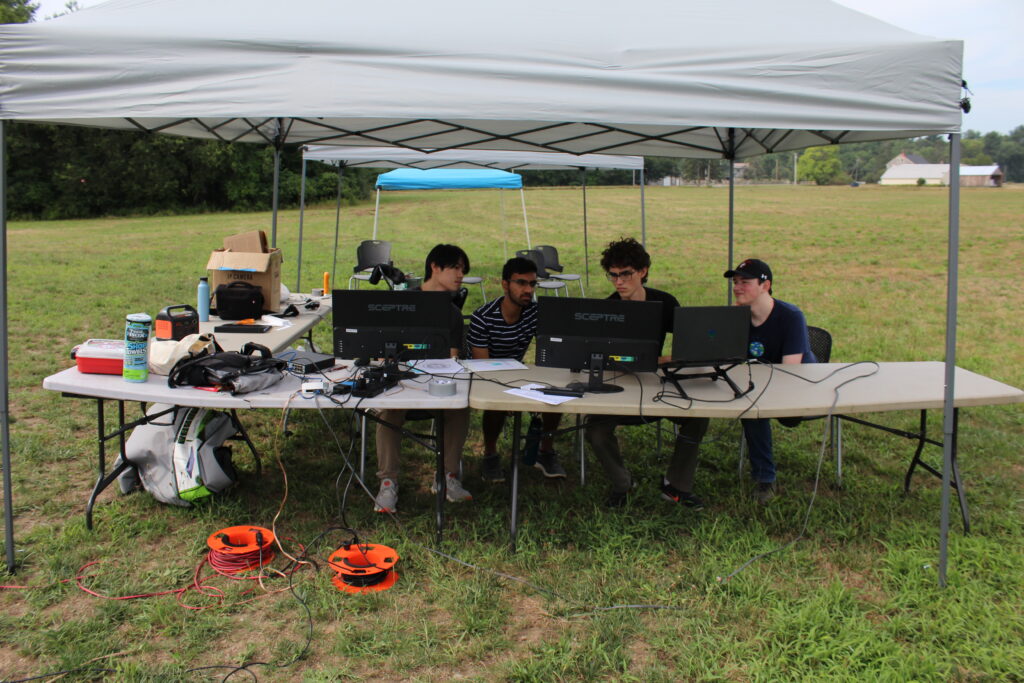
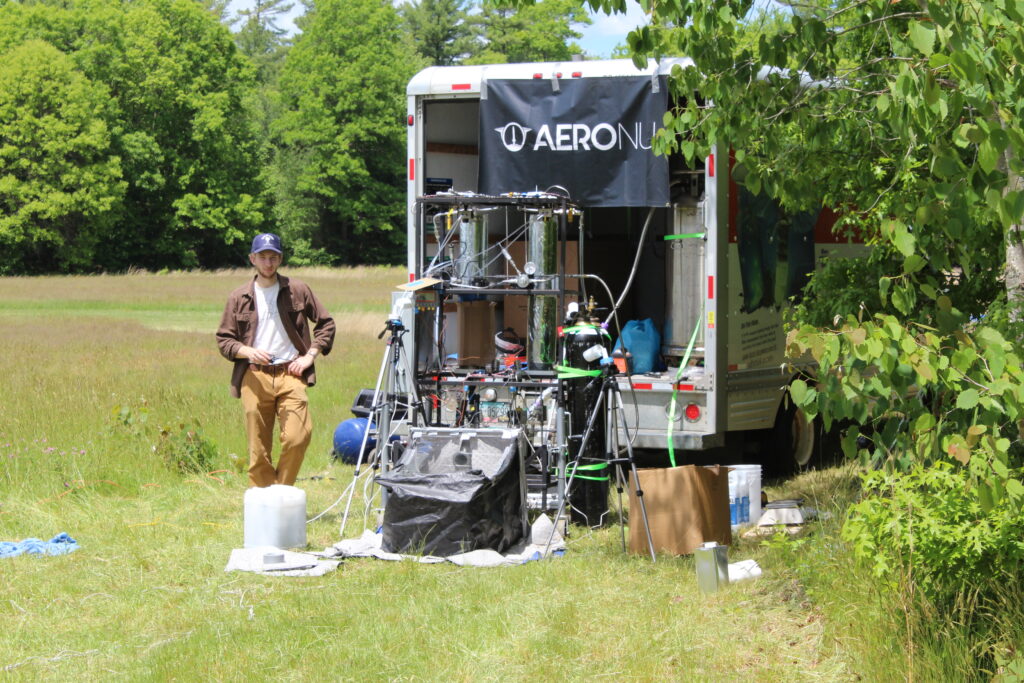
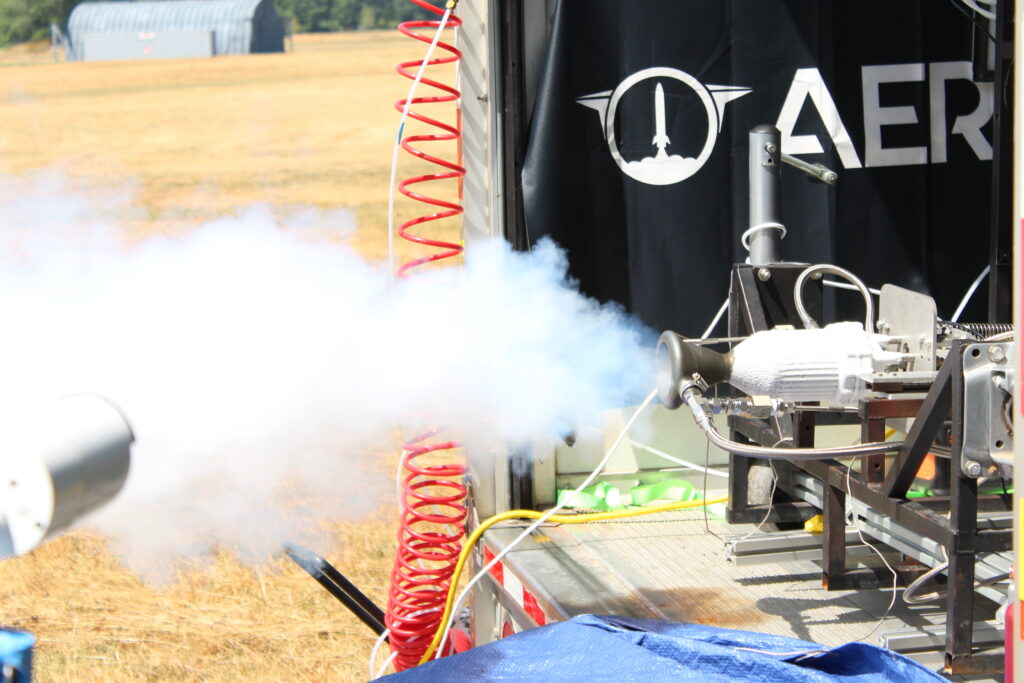
The goals of these tests is often to characterize flow through different parts of the test stand and different conditions. This if often seen through variables such as pressure drop, Cv, mass flow rates, atomization, etc. These are determined experimentally, and help us to perform operations successfully.
To date we have run two static fire tests, neither of which were successful, likely due to hard starts. See the explosive videos below.
Even though not nominally successful, the amount we learn from these is substantial. From these, clear paths forward emerge and we gain intangible insight on how to improve. It’s always inspiring to see the mountain of collaboration and effort that goes into each test, regardless of the degree of success.
Since December 2022 I’ve been leading the project, overseeing key decisions in the development timeline as well as delegating numerous sub-systems including: a swirl injector, automated spark igniter, CO2 fire suppression, and a motor-controlled proportioning valve.
A key part of keeping the project running is education. Many of the systems we work on require in-depth knowledge of fluids, thermodynamics, etc. Unfortunately, most students aren’t exposed to these concepts academically until late in their education. As a result, we make an effort to continually support and teach our newer members so that they can contribute.